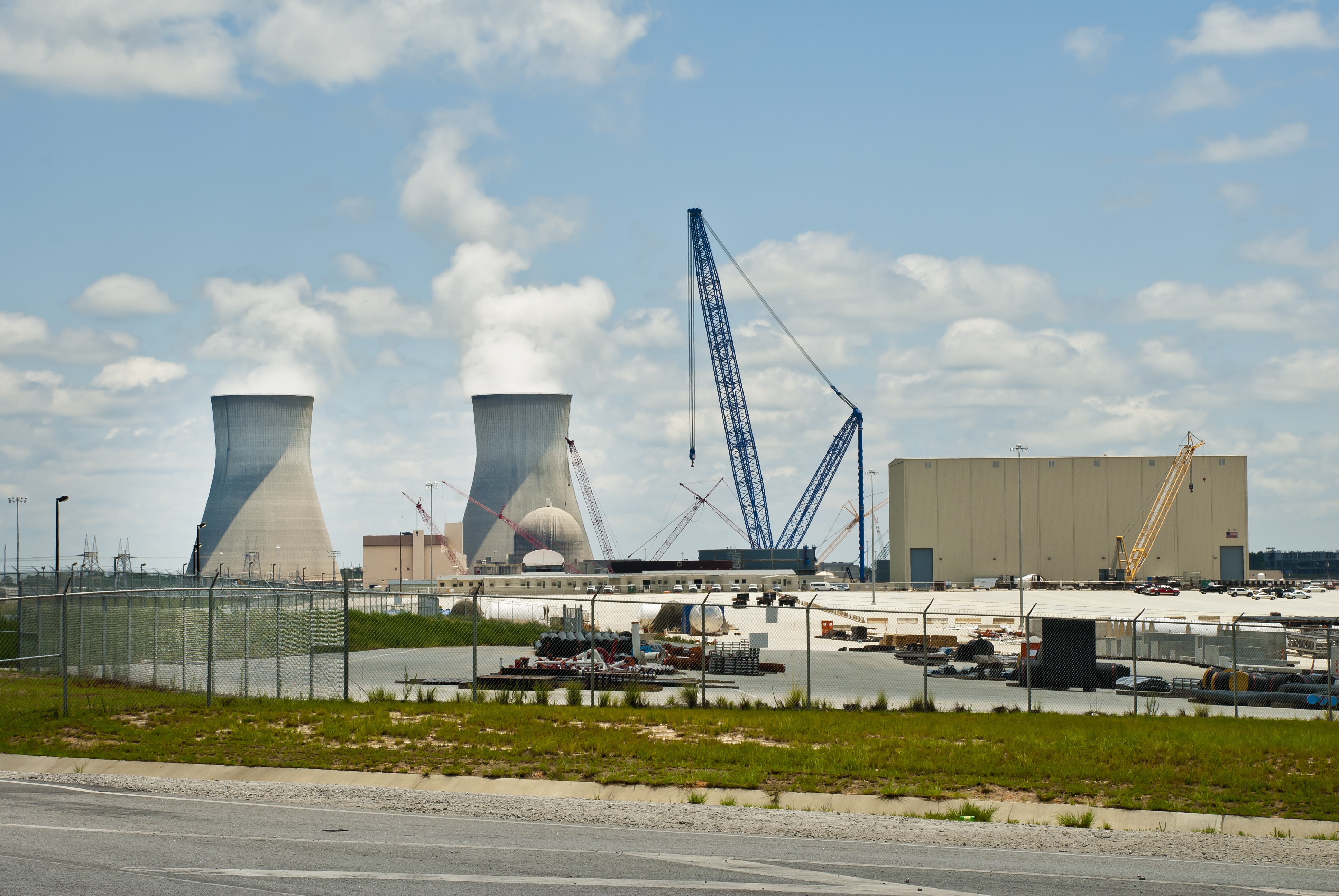
“Joyce and their representative, Sell Industrial, were very helpful throughout the design and build process. We chose Joyce because they were very responsive during the bid evaluation and offered the range and flexibility we needed”
Steve Agace
Operations Manager
Holtec International
HOLTEC INTERNATIONAL
Most operating nuclear reactors do not possess sufficient in-pool storage capacity. For such plants, dry storage and, for the moment an on-site dry storage facility, is the only viable option. Since 1992, Holtec International, a diversified energy technology company, has been engaged in a focused R&D effort to devise, develop, and license the safest and most competent array of components to store and transport spent nuclear fuel. The company’s cask development program has been exclusively geared to develop systems using the multi-purpose canister (MPC) concept. Holtec turned to Joyce/Dayton in 1999 to provide components for the MPC lifting system.
WHY JOYCE JACKSCREWS?
- Safety – An investigation into hydraulic lift systems revealed that in the event of a system failure the safety of the transfer could be compromised. By using an acme thread that will not backdrive, the jackscrews insured that the cask transfer would not experience uncontrolled lowering.
- Cost – The jackscrews were a significant cost-saving feature in the overall bid for the project. Cranes with comparable safety margins can cost as much as five times more than the jackscrews.
- Durability – The Joyce jackscrews require only simple and ordinary maintenance that is easy to perform.
- Overall Performance – The Joyce jackscrews offered better synchronization in this application. Testing prior to application included 125 percent of load tests. The lift elevated the average determined load size plus 25 percent and was required to hold that load for a pre-determined amount of time. The lifting system performed beyond the expectations and proved its capability to maintain the 10-to-1 factor of safety. Since 1873, the Joyce/Dayton Corp., with headquarters based in Dayton, Ohio, has been one of the premier manufacturers of rugged, heavy-duty mechanical and hydraulic lifting and positioning equipment. From leveling log homes and ship dry-dock transfers to stage and ergonomic lifts, Joyce/Dayton has handled the toughest applications imaginable. With unmatched engineering and technical expertise, Joyce can provide custom solutions in a time- and price-sensitive manner turning ideas into working solutions. contact Joyce/Dayton.
Unique Features
- Because of the nature of the spent nuclear fuel, transferring the material is a highly regulated process. The movement of the “shuttle cask” used to transfer the MPC into a storage overpack has to run smoothly and consistently to ensure a safe transfer. The bridge raising the “shuttle cask” has to travel absolutely level.
- The transfer system had to be able to withstand extreme environmental factors such as the impact of a tornado missile – a telephone pole traveling at 300 miles per hour striking the system at a top corner of the bridge
- The first-of-its-kind system had to be approved by the Nuclear Regulatory Commission
- The spent fuel and cask are extremely heavy. The jacks had to be capable of lifting 125 tons or more at an average travel speed of 12 inches per minute. The system is designed with an overall 10 to 1 factor of safety, meaning that the lift must be capable of lifting ten times the expected load without failing
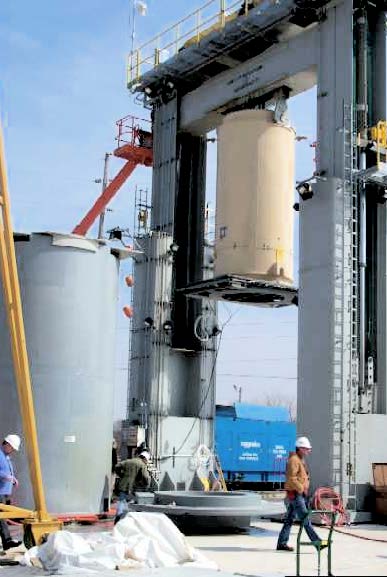
How the system works
There are two 60-foot gantry towers that support a 30-foot horizontal traveling bridge structure. The lifting mechanism is designed with two 21–foot Joyce jackscrews – one in each of the towers – along with Joyce motors, gearboxes and shafts. The Joyce, self-locking jackscrews provide redundancy to the system. The jacks travel length is 234 inches. A full shuttle cask is placed under the transfer system. The bridge is lowered and a cask connector bracket is used to grasp the shuttle cask. The cask is then lifted and a storage cask is slid underneath. The transfer system lowers the MPC from the “shuttle cask” into the storage cask for safekeeping.