Note: An upright jack mounted upside down is still referred to as an upright jack.
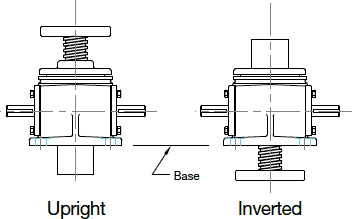
- For an Upright jack:
CCW rotation of right input shaft extending the lifting screw. CW rotation of the left shaft extending lifting screw. - For an Inverted jack:
CW rotation of right input shaft extending lifting screw. CCW rotation of the left shaft extending lifting screw.
Each screw jack and actuator has an inherent number of input shaft turns per inch (TPI) of screw travel. TPI is the result of the jack's gear ratio divided by the lifting screw lead. The TPI can be found on jack specification pages at the beginning of many product sections. A model WJT242 has a TPI of 96. If 350 RPM is applied to the input shaft, the resultant linear speed of travel is 350/96 or 3.65 inches per minute. JAX® Online software automatically calculates travel speeds for you.
All Joyce machine screw jacks and ComDRIVEs®, ball screw jacks and ComDRIVEs®, bevel ball actuators, integrated actuators, and electric cylinders are lubricated with an extreme pressure NLGI grade #1 grease before leaving the factory.
Bevel gear jacks are lubricated with NLGI grade #1 grease and oil. The upper bearing and jackscrew are grease lubricated while the remaining internal components are oil lubricated. They are grease lubricated prior to shipment; however oil must be added to the unit prior to operation.
The following standard end conditions are available on Joyce/Dayton screw jacks:
Type 1
plain turned end
Type 2
load pad with mounting holes
Type 3
male threaded end
Type 4
male clevis end
Contact [email protected] for information about custom end conditions.
- Standard clevis mounting position – the hole in the clevis end is parallel with the worm input shaft.
- Optional mounting position – the hole in the clevis end is perpendicular to the worm input shaft.
- Standard load pad mounting position – the holes on the load pad are on the jack centerlines.
- Optional load pad mounting position – the holes on the load pad end straddle the jack centerlines.
Yes. When freedom of movement in two axes is required, a double clevis jack may be specified. Double clevis jacks are always made from upright jacks. Stroke lengths are limited based compression loads. See the chart at the end of the entry. Contact Joyce/Dayton with application details.
- Double clevis jacks incorporate a clevis machined or pinned onto the screw end and also a clevis welded to the protection tube. Screw travel is limited. Contact [email protected] for more information.
- Electric cylinders, integrated actuators, multipurpose actuators, and solar actuators are also available with a clevis on both ends
Machine Screw Jack |
Max Load |
Max Rise at full load in Compression |
Reduced Load |
Max Rise at Reduced Load in Compression |
1/4-ton | 500 LB | 7.00 Inches | 500 LB | 7.00 Inches |
1/2-ton | 1000 LB | 9.00 Inches | 1000 LB | 9.00 Inches |
1-ton | 2000 LB | 8.00 Inches | 1500 LB | 10.00 Inches |
2-ton | 4000 LB | 12.00 Inches | 3000 LB | 14.00 Inches |
3-ton | 6000 LB | 12.00 Inches | 3000 LB | 14.00 Inches |
5 ton | 10,000 LB | 17.00 Inches | 6500 LB | 22.00 Inches |
10-ton | 20,000 LB | 23.00 Inches | 12,000 LB | 31.00 Inches |
15-ton | 30,000 LB | 26.00 Inches | 16,000 LB | 37.00 Inches |
20-ton | 40,000 LB | 29.00 Inches | 21,000 LB | 42.00 Inches |
25-ton | 50,000 LB | 47.00 Inches | 37,000 LB | 56.00 Inches |
30-ton | 60,000 LB | 47.00 inches | 37,000 LB | 56.00 Inches |
35-ton | 70,000 LB | 69.00 Inches | 62,000 LB | 74.00 Inches |
50-ton | 100,000 LB | 90.00 Inches | 94,000 LB | 93.00 Inches |
Self-locking is a term used to describe jacks that require power to move in either direction. They hold their position when power to the system is off.
A brake is required on the input shaft of any jack that may lower under load (ball screw jacks, WJ500 jacks, double-lead Acme screw jacks, electric cylinders that are more than 30% efficient, and some integrated actuators).
Standard jacks and actuators are not designed for dynamic side loads. The load must be positioned axially. Static side loads are limited. Contact [email protected] for technical assistance.
In machine screw jacks there are two types of backlash: worm to wormgear backlash (typically 8-15° worm rotation), and lifting screw to nut backlash, sometimes called endplay (up to 0.020 inches on new standard jacks). These values are automatically calculated for all products sized in Joyce's free JAX® Online Software for all products. Contact [email protected] for more information.
In machine screw jacks there are two types of backlash: worm to wormgear backlash (typically 8-15° worm rotation), and lifting screw to nut backlash, sometimes called endplay (up to 0.020 inches on new standard jacks). These values are automatically calculated for all products sized in Joyce's free JAX® Online Software for all products. Contact [email protected] for more information.
Yes, screw backlash can be adjusted on translating and keyed style machine screw jacks via one of the following anti-backlash options: standard split-nut design; A90 external nut adjustment; or A95 design. Contact [email protected] for more information.
The deviation from the mathematical lead expressed in inches per foot cumulative.
Rolled Acme screws have up to .010 in/ft cumulative error, milled Acme screws have up to 0.003 in/ft cumulative error; and ball screws have up to 0.007 in/ft cumulative error. Contact [email protected] for more information.
The level to which products can be serviced in the field varies from product to product. Refer to the product Operation & Maintenance Manuals or contact [email protected] for more information.
Motor options vary among product lines. Customers can use AC 3-phase, AC single-phase, DC motors, international voltage motors and others. Let us know your requirements.
No. Limit switches on multipurpose actuators (MA) are preset at the factory. All other limit switches must be set according to specific directions.
- Shaft-mounted rotary cam limit switches must be set to the required positions during installation.
- Closed height dimensions may increase when boots are added.
- The customer must specify boot collar diameter when ordering bellows boots for KFTN jacks.
- Zippered boots are also available.
- Special boot material is available.
- Horizontal screw applications may require boot guides.
Contact [email protected] for more information.
Stainless steel jacks are inherently corrosion resistant. All exposed surfaces are stainless steel and aluminum bronze. Most other jacks can be modified with special finishes, coatings, and seals. Contact [email protected] with your requirements.
Follower nut assemblies allow customers to gauge the wear on the wormgear screw thread of translating jacks and on the traveling nut screw thread of KFTN jacks. This allows customers to replace the nut before its threads wear too thin to support the design load. These assemblies generally consist of a gear nut or traveling nut pinned to a second nut of dissimilar material. A preset gap separates the two nuts. As the wormgear or traveling nut threads wear, the preset gap narrows. The assembly is replaced when the gap measurement reaches the design limit. Follower nut assemblies are designed for specific applications. Contact [email protected] for more information.