Ball Screw Jacks
About Ball Screw Jacks
Joyce worm gear ball screw jacks lift and precisely position loads up to 50-tons. Upright or inverted jacks operate at full capacity in tension or compression. Select from standard lead (WB, WBL) and high lead (HWB, HWBL) models to meet your travel speed and ball nut life requirements. These ball screw jacks require up to two-thirds less input torque to move the load than similarly rated machine screw jacks. They require a brake motor or external locking device to hold position.
- Alloy steel input shafts
- Aluminum bronze worm gears
- Tapered or ball thrust bearings
- Choose one of four standard end conditions
- Protective boots available
- Oversized ball bearings available to limit end play
- Joyce/Dayton can customize to your specifications
- Custom finishes available
Parts list and exploded views are included in the O&M Manual. Serial numbers are attached to the product housing.
Product Media
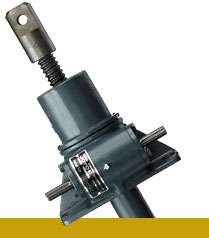
Available Models
Joyce/Dayton provides motor controls ranging from simple Motor Starters to complex positioning systems and Custom controls. Every system that is powered by an electric motor requires a control system. At Joyce, we know that choosing the best option can sometimes be a challenge. That’s why our Engineers are available to help you through the process.
Boots and special finishes are available for Joyce Ball Screw Jacks. Choose from a variety of boot materials and designs for the jacks you select (translating or KFTN). Joyce offers premium finishes, outdoor paint process, and custom finishes to meet your specifications. We have a hassle-free process for delivering what you need.
What you need to know to specify ball screw jacks in industrial applications
Ball Screw Jacks are rated based on their static thrust capacity from 1-ton to 50-tons. But the selection of the best jack for the application requires further consideration.
- When jacks are loaded in compression one must consider the load carrying capacity of the lifting screw (column load). How high do you need to lift the load? Choose a jack whose lifting screw is stout enough to handle the load at full rise.
- Consider the travel speed of the DYNAMIC load. The speed at which the load will be moved is a limiting factor. How fast do you need to move the load? Sometimes high lead ball screw jacks or bevel ball actuators are a better choice in a given application.
- How frequently will the jack need to move the load? Ball screw jacks are much more efficient than machine screw jacks, so heat is less of a factor in their operation, yet cycles for ball screw jacks must include some periods of rest.
- You can choose a ball screw jack that meets specific life requirements. A calculated ball nut life (in inches) can be established for ball screw jacks based on the load, and duty cycle. Use the JAX® Online software to determine this.
Once loads, duty cycles, and travel speeds are established, designers must select which jack design to use.
- Translating Design Jacks are most often selected. With this design, a driven input worm acts on an internal worm gear causing the lifting screw to extend or retract. Operation requires that rotation of the lifting screw be prevented. This rotation it restrained whenever two or more jacks are tied to the same load.
- Ball screw jacks cannot be keyed for non-rotation the same way that machine screw jacks are keyed. Contact Joyce for a design solution if you need a keyed ball screw jack.
- Keyed for Traveling Nut Design (KFTN) jacks are another option. These jacks have a fixed length lifting screw that rotates. Loads are attached to a flanged “traveling” ball nut that translates up and down the length of the rotating screw. This type of jack is ideal for applications that cannot accommodate a screw protection tube or that require a flush mount
Special features inherent in wormgear ball screw jacks.
Ball screw jacks include ball nuts that are about 90% efficient so the jacks require much less energy to lift an equal load than their machine screw jack counterpart. They are NOT self-locking so a brake motor needs to be included in the drive system and hand wheels are not a recommended option.
Take the work out of using screw jacks in systems
Joyce/Dayton screw jacks and lifting systems offer wide-ranging lifting and positioning solutions for diverse industries. Our robust jacks reliably move and accurately position loads up to 250-tons. Joyce configures jacks with components such as motors, gear reducers, shafting, coupling, and motion control devices to create complete multi-jack systems.
Tell us what you need or use our exclusive JAX® Online software (it’s free). We will put together complete systems with single or multiple screw jacks for you. The software is great because it calculates motor horsepower and shaft diameters and torques. There are several common arrangements, but the program is flexible and allows you to design what you need.
Where are worm gear ball screw jacks used?
Worm gear ball screw jacks are fast and efficient. They can accurately position and hold loads up to 50-tons. Examples include: Platform lifts, Damper adjustments, Ergonomic lifts, Maintenance lifts, Roll adjustments, Earth Station Antennas, Solar Trackers, Conveyor adjustments, Packaging equipment, and Gate adjustments.
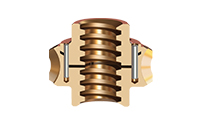
Ball Screw Options
- Right hand thread standard
- Left hand thread available on many models
- Special pitch/lead available
- Special finishes available
- Special machining options
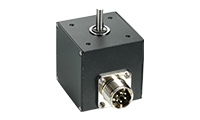
Encoders
- Standard 200 or 1024 PPR
- Quadrature wave form
- Stainless steel encoder
- Absolute encoder
- Encoders
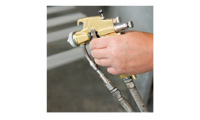
Finishes
- Enamel finish (standard)
- Epoxy finish
- STEEL IT® epoxy
- Outdoor paint process
- Custom finishes available
- Anodized (250-lb to 1-ton)
- Nickel, Xylan®, Armoloy®
- Finishes
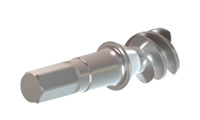
Input Shaft (worm)
- Square or hex to fit tool
- Special lengths
- 17-4 stainless steel available
- Metric diameters available
- One side can be cut off
- Other modifications available
- Input shaft cover available
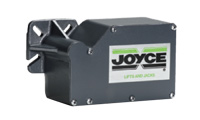
Limit Switches
- Rotary cam (2-4 switches)
- SPDT standard
- DPDT available
- Explosion proof available
- Limit Switches
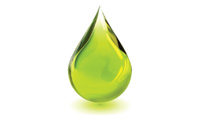
Lubrication
- Standard grease temperature range (40°F to 220°F)
- Low temperature option
- High temperature option
- Food grade option
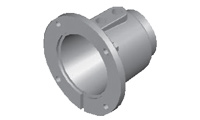
Motor Mounts
- NEMA mounts available on 2-ton to 20-ton wormgear jacks and electric cylinders
- NEMA mounts included on integrated actuators
- Servo motor mounts available on 2-ton to 10-ton jacks and electric cylinders, special mounts available
- Custom mounts available
- Motor Mounts and Stock Motors
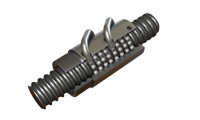
Oversized Ball Bearings
- Available for ball screw jacks
- Limits screw backlash to 0.003"
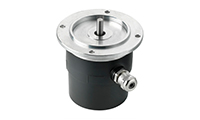
Potentiometers
- 0-10V (POTA)
- 4-20mA (POTB)
- 0-10V with limit switches (POTC)
- 4-20mA with limit switches(POTD)
- IP65
- Potentiometers
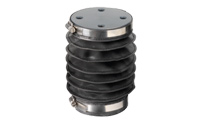
Protective Boots
- Protection from dirt and dust
- Guard against moisture
- Guard against corrosive contaminants
- Neoprene coated nylon (std)
- Special materials available
- Boot Material Chart
- Protective Boots
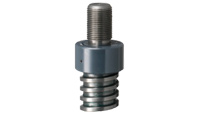
Screw Stops
- Standard on ComDRIVEs
- Adjustable
- Bolt- on
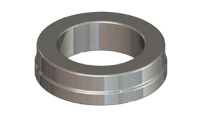
Thrust Rings
- Used in applications where static loads exceed jack capacity
Sample Part Number:
Click on the part number to reveal additional informaton about jack designs and shaft codes.
Model Number
1-Ton Standard | 2-Ton Standard | 2-Ton Reverse Base Standard | 5-Ton Standard | 10-Ton Standard | 10-Ton Heavy Duty | 20-Ton Standard | 30-Ton Standard | 50-Ton Standard |
---|---|---|---|---|---|---|---|---|
WBL51 WBL201 |
WB62 WB122 WB242 |
RWB62 RWB122 RWB242 |
WB65 WB125 WB245 |
WBL810 WBL2410 |
WB810 WB2410 |
WB820 WB2420 |
WB1130 WB3230 |
WB1150 WB3250 |
1-Ton Heavy Duty | 2-Ton High Lead | 2-Ton Reverse Base High Lead | 5-Ton High Lead | 10-Ton Standard High Lead | 10-Ton Heavy Duty High Lead | 50-Ton Reverse Base | ||
WB51 WB201 |
HWB62 HWB122 HWB242 |
RHWB62 RHWB122 RHWB242 |
HWB65 HWB125 HWB245 |
HWBL810 HWBL2410 |
HWB810 HWB2410 |
RWB1150 RWB3250 |
Important Note: *Not self-locking, may lower under load. Brake motors or external locking systems are required.
H: indicates High lead (2-ton, 5-ton and 10-ton only).
R: Reverse Base Jack (2-ton and 50-ton only).
Jack Configuration
![]() |
![]() |
U=Upright |
I=Inverted |
End Conditions
![]() |
![]() |
![]() |
![]() |
1=T1 |
2=T2 |
3=T3 |
4=T4 |
Jack Designs
![]() |
![]() |
![]() |
![]() |
![]() |
S=Translating |
K=Keyed for Non Rotation** |
N=Traveling Nut |
D=Double Clevis |
R=KFTN Trunnion* |
*Standard trunnion mounts available on 2-ton through 20-ton jacks.
**Keyed for non-rotation is not a standard option. Contact Joyce/Dayton with your requirements.
Ball Screw Jack Rise
Rise is travel expressed in inches and not the actual screw length.
Left Side Shaft Code |
Right Side Shaft Code |
XXXX=Remove |
XXXX=Remove |
Optional Shaft Codes
Screw Stops and Boots
Screw stops are optional on ball screw jacks. When specified, the closed height of the jack and/or the protection tube length may be increased. When boots are added to ball screw jacks, the closed height of the jack may be increased.
Geared Potentiometers
POTA=0-10V (IP65)
POTB=4-20MA (IP65)
POTC=0-10V w/2 switches*
POTD=4-20MA w/2 switches*
*Optional IP65 rating available
Encoders and Electronic Limit Switches
ENCX=Encoder
ELS2=2 Position Electronic Switch
ELS4=4 Position Electronic Switch
ELS6=6 Position Electronic Switch
Motor for Systems and Direct Drive
- All standard motors are 3-phase, 208-230/460 VAC or 230/460 VAC. Other motor options are available. Specify the appropriate motor size from the chart on the right.
- Refer to the "Additional Options" chart on the preceding page as needed.
- Brake motors (M2) are recommended for jacks that are not self-locking, and jacks with double lead screws.
- If the motor frequency will be varied to provide a "soft" start an inverter duty motor may be required.
Motors
Size | Code |
---|---|
1/4 HP | K |
1/3 HP | A |
1/2 HP | B |
3/4 HP | C |
1 HP | D |
1-1/2 HP | E |
2 HP | F |
3 HP | L |
5 HP | G |
7-1/2 HP | H |
10 HP | I |
15 HP | J |
Motor Mounts
Ordering Example:
MMA A (Motor code from chart above)
MMA=56C
MMB=140TC
MMC=180TC
MMD=210TC
Standard motor adapters are aluminum
Mechanical Limit Switches
Ordering Example:
LA (Models) 1(Number of DPDT Switches) 3(Available Positions)
Model | Code | Available Positions | |||||||||
---|---|---|---|---|---|---|---|---|---|---|---|
LS7-402 | LI |
Number of DPDT Switches NOTE: Will always be 0 for LS7 models |
1 | 2* | 3 | 4 | 5 | 6* | 7 | 8 | |
LS8-402 | LA | Left Side Shaft Options | ![]() |
![]() |
![]() |
![]() |
![]() |
![]() |
![]() |
![]() |
|
LS8-504 | LB | ||||||||||
LS9-502 | LC | ||||||||||
LS9-503 | LD | Right Side Shaft Options | ![]() |
![]() |
![]() |
![]() |
![]() |
![]() |
![]() |
![]() |
|
LS9-504 | LE | ||||||||||
LS9-505 | LF | ||||||||||
LS9-506 | LG |
These positions are not standard. Contact Joyce/Dayton with your requirements. |
|||||||||
LS9-507 | LH |
Additional Options
- X=Standard Jack, no additional options
- S=Additional Specification Required (comment as necessary)
Anti-Backlash
- A=Split Nut
- A90=A90 Design
- A95=A95 Design
Protective Boots
- B=Protective Boot
- D=Dual Protective Boot
Finishes
- F1=Do Not Paint
- F2=Epoxy Paint
- F3=Outdoor Paint Process
Motor Options
- M1=Less Motor
- M2=Brake Motor
- M3=Single Phase Motor (120VAC)
- M4=50Hz Motor
Grease/Seals
- H1=High Temperature Operation
- H2=Food Grade
Screw Stops
- ST0=Extending
- ST1=Retracting
- ST2=Both
- Specify as many options as needed
Model | Capacity | Screw Diameter (inches) | Thread Pitch/ Lead |
Worm Gear Ratio | Worm Shaft Turns for 1" Travel |
Tare Torque (Inches Lbs.) | Starting Torque (Inches Lbs.) | Operating Torque (Inches Lbs.) | Efficiency Rating % Approx | Screw Torque (Inches Lbs.) | Worm Holding (Inch Lbs.) | Ball Nut Life at Rated Load (Inch Screw Travel x 1000) |
Basic Jack Weight (Lbs.) | Jack Weight per Inch Travel (Lbs.) |
---|---|---|---|---|---|---|---|---|---|---|---|---|---|---|
WBL51 | 1 ton | 3/4 | 0.2 | 5:1 | 25 | 3 | .014W* | .012W* @ 500 RPM |
51.7 | .035W* | .006W* | 108 | 8 | 0.25 |
WBL201 | 1 ton | 3/4 | 0.2 | 20:1 | 100 | 3 | .005W* | .004W* @ 500 RPM |
38.5 | .035W* | .002W* | 108 | 8 | 0.25 |
WB51 | 1 ton | 3/4 | 0.2 | 5:1 | 25 | 3 | .014W* | .012W* @ 500 RPM |
51.7 | .035W* | .006W* | 858 | 8 | 0.25 |
WB201 | 1 ton | 3/4 | 0.2 | 20:1 | 100 | 3 | .005W* | .004W* @ 500 RPM |
38.5 | .035W* | .002W* | 858 | 8 | 0.25 |
(R)WB62 | 2 ton | 1 | 0.25 | 6:1 | 24 | 4 | .015W* | .013W* @ 500 RPM |
52.1 | .044W* | .007W* | 642 | 18 | 0.4 |
(R)WB122 | 2 ton | 1 | 0.25 | 12:1 | 48 | 4 | .009W* | .007W* @ 500 RPM |
47.2 | .044W* | .004W* | 642 | 18 | 0.4 |
(R)WB242 | 2 ton | 1 | 0.25 | 24:1 | 96 | 4 | .006W* | .004W* @ 500 RPM |
39.3 | .044W* | .002W* | 642 | 18 | 0.4 |
(R)HWB62 | 2 ton | 1 | 1 | 6:1 | 6 | 4 | .064W* | .051W* @ 500 RPM |
52.1 | .177W* | .020W* | 190 | 18 | 0.4 |
(R)HWB122 | 2 ton | 1 | 1 | 12:1 | 12 | 4 | .041W* | .028W* @ 500 RPM |
47.2 | .177W* | .020W* | 190 | 18 | 0.4 |
(R)HWB242 | 2 ton | 1 | 1 | 24:1 | 24 | 4 | .028W* | .017W* @ 500 RPM |
39.3 | .177W* | .014W* | 190 | 18 | 0.4 |
WB65 | 5 ton | 1 1/2 | 0.474 | 6:1 | 12.66 | 10 | .030W* | .025W* @ 300 RPM |
51.1 | .084W* | .013W* | 1015 | 42 | 0.7 |
WB125 | 5 ton | 1 1/2 | 0.474 | 12:1 | 25.33 | 10 | .019W* | .014W* @ 300 RPM |
45.7 | .084W* | .007W* | 1015 | 42 | 0.7 |
WB245 | 5 ton | 1 1/2 | 0.474 | 24:1 | 50.66 | 10 | .013W* | .008W* @ 300 RPM |
37.2 | .084W* | .004W* | 1015 | 42 | 0.7 |
HB65 | 5 ton | 1 1/2 | 1.0 | 6:1 | 6 | 10 | .065W* | .052W* @ 300 RPM |
51.1 | .177W* | .033W* | 512 | 42 | 0.7 |
HB125 | 5 ton | 1 1/2 | 1.0 | 12:1 | 12 | 10 | .041W* | .029W* @ 300 RPM |
45.7 | .177W* | .020W* | 512 | 42 | 0.7 |
HB245 | 5 ton | 1 1/2 | 1.0 | 24:1 | 24 | 10 | .029W* | .018W* @ 300 RPM |
37.2 | .177W* | .014W* | 512 | 42 | 0.7 |
WBL810 | 10 ton | 1 1/2 | 0.474 | 8:1 | 16.88 | 20 | .022W* | .019W* @ 200 RPM |
50.7 | .084W* | .010W* | 127 | 58 | 0.9 |
WBL2410 | 10 ton | 1 1/2 | 0.474 | 24:1 | 50.66 | 20 | .010W* | .008W* @ 200 RPM |
40.3 | .084W* | .004W* | 127 | 58 | 0.9 |
HWBL810 | 10 ton | 1 1/2 | 1.0 | 8:1 | 8 | 20 | .047W* | .039W* @ 200 RPM |
50.7 | .177W* | .024W* | 64 | 58 | 0.9 |
HWBL2410 | 10 ton | 1 1/2 | 1.0 | 24:1 | 24 | 20 | .024W* | .016W* @ 200 RPM |
40.3 | .177W* | .012W* | 64 | 58 | 0.9 |
WB810 | 10 ton | 2 | 0.5 | 8:1 | 16 | 20 | .023W* | .019W* @ 200 RPM |
50.7 | .088W* | .009W* | 729 | 62 | 1.4 |
WB2410 | 10 ton | 2 | 0.5 | 24:1 | 48 | 20 | .011W* | .008W* @ 200 RPM |
40.3 | .088W* | .003W* | 729 | 62 | 1.4 |
HWB810 | 10 ton | 2 | 1.0 | 8:1 | 8 | 20 | .047W* | .039W* @ 200 RPM |
50.7 | .177W* | .018W* | 1423 | 62 | 1.4 |
HWB2410 | 10 ton | 2 | 1.0 | 24:1 | 24 | 20 | .023W* | .016W* @ 200 RPM |
40.3 | .177W* | .006W* | 1423 | 62 | 1.4 |
WB820 | 20 ton | 2 1/4 | 0.5 | 8:1 | 16 | 40 | .024W* | .020W* @ 200 RPM |
47.4 | .088W* | .009W* | 121 | 105 | 2.6 |
WB2420 | 20 ton | 2 1/4 | 0.5 | 24:1 | 48 | 40 | .012W* | .009W* @ 200 RPM |
35 | .088W* | .003W* | 121 | 105 | 2.6 |
WB1130 | 30 ton | 3 | 0.66 | 11:1 | 16.67 | 60 | .027W* | .020W* @ 200 RPM |
48 | .117W* | .009W* | 343 | 220 | 3.2 |
WB3230 | 30 ton | 3 | 0.66 | 32:1 | 48.48 | 60 | .016W* | .009W* @ 200 RPM |
35 | .117W* | .003W* | 343 | 220 | 3.2 |
(R)WB1150 | 50 ton | 4 | 1.0 | 11:1 | 11 | 100 | .038W* | .029W* @ 200 RPM |
49.3 | .117W* | .013W* | 614 | 460 | 4.8 |
(R)WB3250 | 50 ton | 4 | 1.0 | 32:1 | 32 | 100 | .020W* | .012W* @ 200 RPM |
37.5 | .117W* | .005W* | 614 | 460 | 4.8 |
Important Note: Ball Screw Jacks are not self-locking. Brake motors or external locking systems are required.
(R): Reverse Base Jack.
*W: Load in pounds.
Tare Torque: Initial torque to overcome seal and normal assembly drag. (This value must be added to starting torque or operating torque values.)
Starting Torque: Torque value required to start moving a given load (dissipates to operating torque values once the load begins moving).
Operating Torque: Torque required to continuously raise a given load at the input RPM listed. NOTE: If your actual input RPM is 20% higher or lower than the listed RPM, please refer to our JAX program to determine actual torque values at your RPM.
Screw Torque: Torque required to resist screw rotation (Translating Design Jacks) and traveling nut rotation (Keyed for Traveling Nut Design Jacks).
Worm Holding Torque: Torque required to prevent input shaft (worm) from backdriving.
Lead: The distance traveled axially in one rotation of the lifting screw.
Pitch: The distance from a point on a screw thread to a corresponding point on the next thread, measured axially.